Confira como a mamadeira da Lolly Baby é fabricada
Exame.com visitou a fábrica da Lolly Baby, em Capivari, para mostrar o passo-a-passo da produção de uma mamadeira
Karin Salomão
Publicado em 24 de outubro de 2014 às 08h34.
Última atualização em 13 de setembro de 2016 às 15h00.
São Paulo - A Lolly Baby, fabricante de produtos para bebês há 24 anos, é a terceira no Brasil em faturamento de produtos para bebês, como mamadeiras, chupetas, colheres, entre outros. Já em número de unidades vendidas, é a segunda no país. Nos últimos 10 anos, cresceu 25 vezes e pretende se tornar a líder de mercado até 2020. Exame.com foi até a fábrica da empresa, em Capivari, interior de São Paulo, para ver como é produzida a mamadeira do seu filho ou filha. Este era o primeiro dia de fabricação deste produto, que chegará ao mercado nos próximos meses.
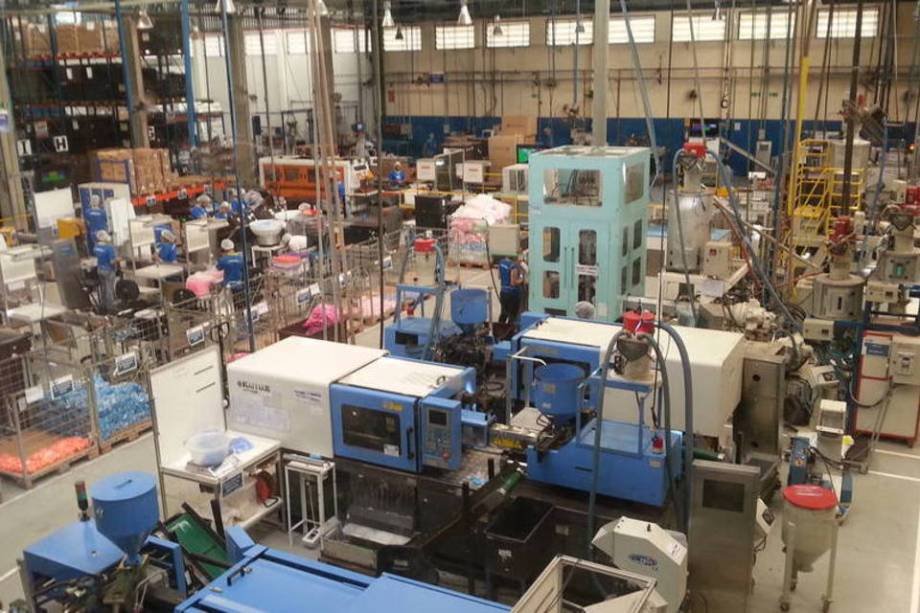
2 /20(Karin Salomão/Exame.com)
A primeira coisa a entender é que, na fábrica da Lolly Baby, não há uma linha de montagem. Como há mais de 700 produtos diferentes, não seria possível fabricar um por vez, em uma linha única. Há diversas máquinas espalhadas na planta, cada uma produzindo uma parte diferente. No fim, as partes serão unidas, embaladas e enviadas às lojas. No total, são 204 funcionários, trabalhando em três turnos para que a fábrica fique ativa 24 horas por dia.
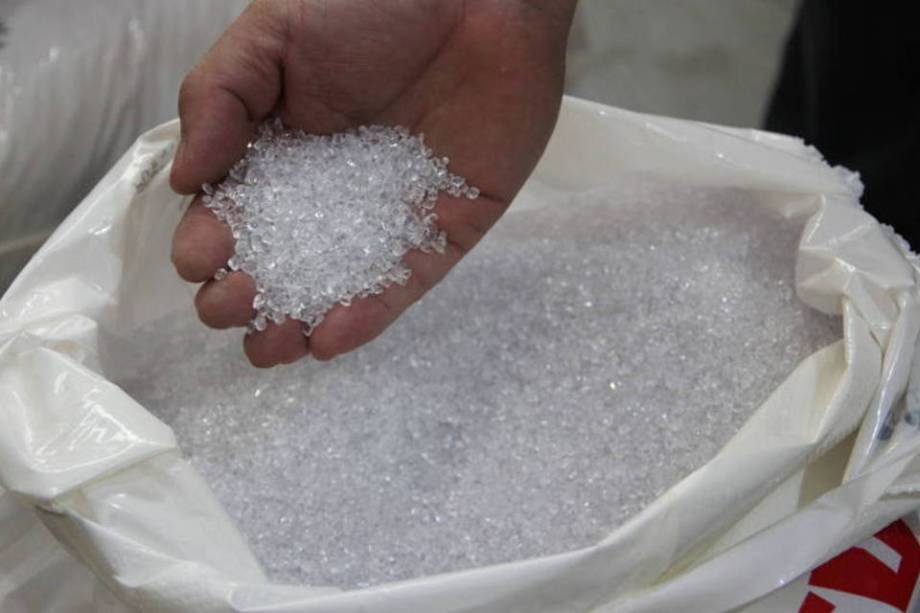
3 /20(Karin Salomão/Exame.com)
O primeiro passo é a preparação e tingimento do material. A Lolly usa, desde 2010, a resina Tritan em alguns de seus produtos mais premium. É um co-poliéster mais difícil de ser processado, e também mais brilhante e resistente. É uma das poucas empresas a usar esse material, comprado da Eastman, na América Latina. A cada seis meses, a fábrica usa 20 toneladas de Tritan na fabricação de todos os produtos. Como cada mamadeira pesa 24 gramas, é possível fabricar 833 mil mamadeiras, por exemplo. Também usam um polipropileno, outra matéria-prima, da Braskem.
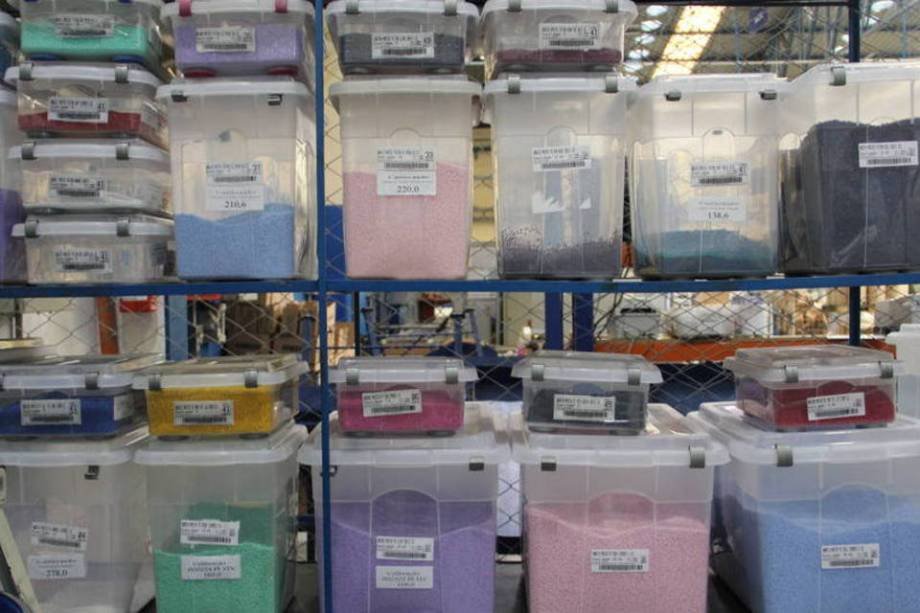
4 /20(Karin Salomão/Exame.com)
A resina tritan foi usada em quase todas as peças da mamadeira. A diferença é apenas o tingimento de cada parte e algumas variações na fabricação. Para atingir o tom certo de azul – ou rosa, roxo, vermelho, a proporção é de 2% de resina colorida para 98% de material transparente.
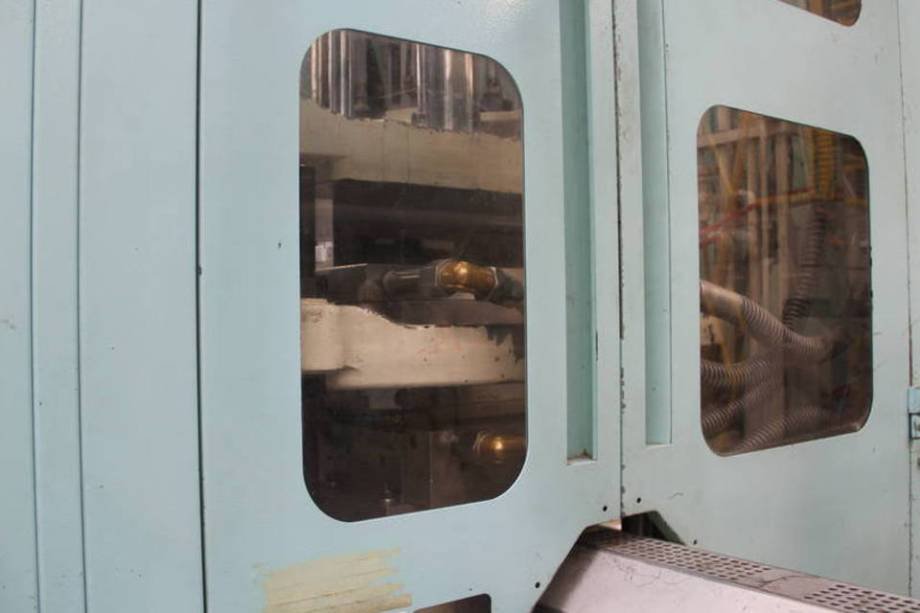
5 /20(Karin Salomão/Exame.com)
Antes de ser moldado no corpo da mamadeira, o material passa seis horas secando a 80°C, para retirar toda umidade. Depois, é derretido a 230°C e vira uma pasta.
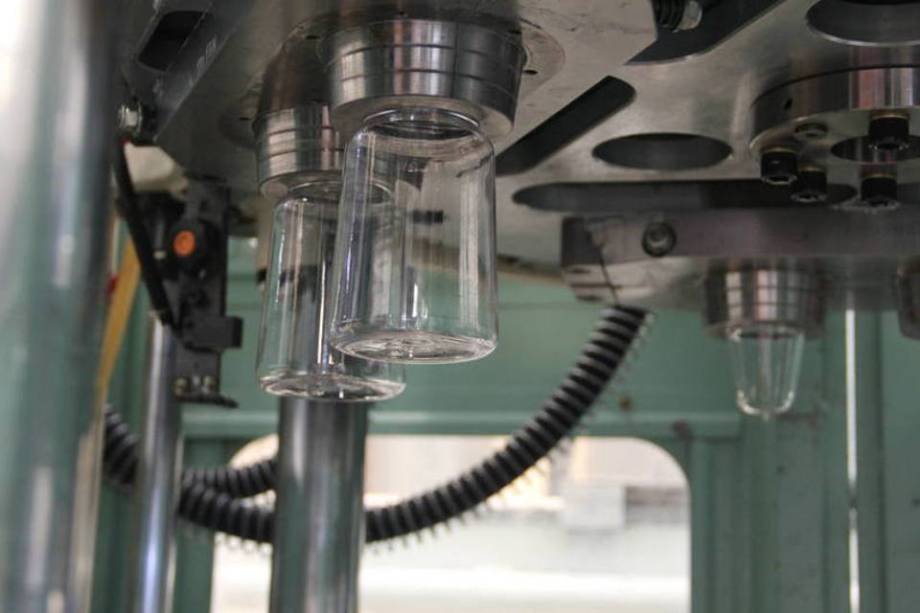
6 /20(Karin Salomão/Exame.com)
Depois, a matéria-prima é injetada em uma forma e soprada a uma pressão de 8 bar para formar a mamadeira. Ao fundo, o material antes de ser soprado na forma do frasco, que já está pronto no primeiro plano.
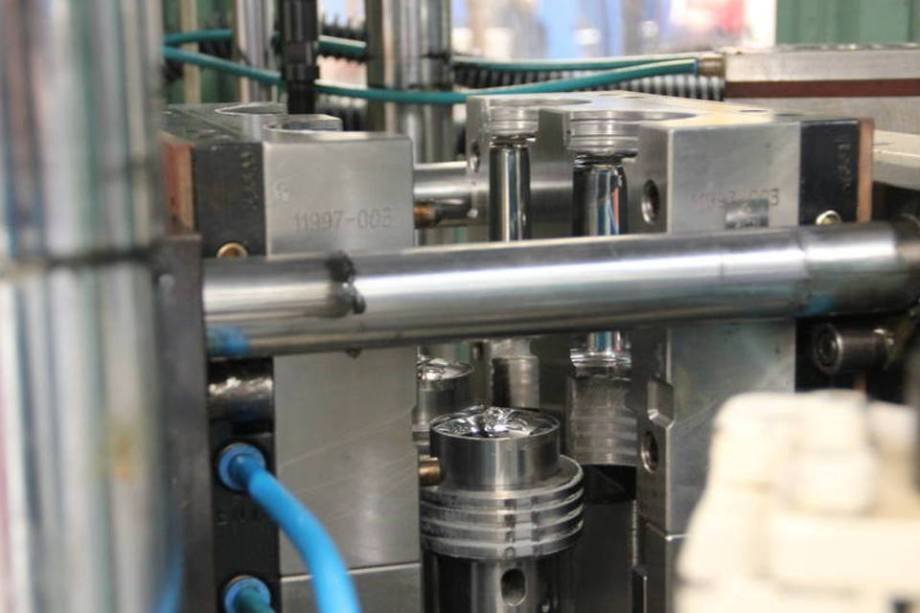
7 /20(Karin Salomão/Exame.com)
Para o material se solidificar, água gelada a 18°C passa pelo molde através das mangueiras azuis e resfria o material.
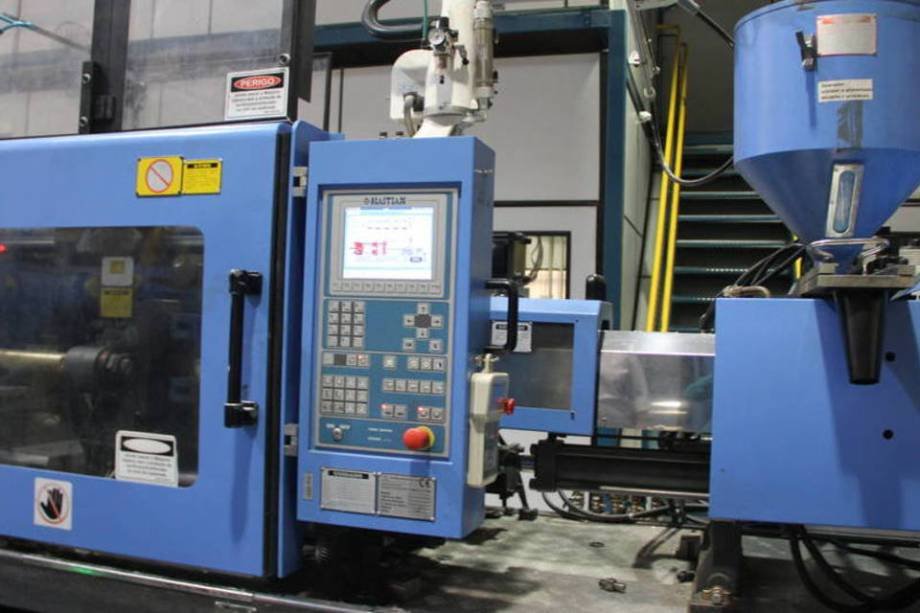
8 /20(Karin Salomão/Exame.com)
O processo de fabricação do capuz – a tampa da mamadeira - é bastante parecido. Apenas a secagem por horas não é necessária. A pasta azul, já tingida e derretida, é injetada no molde a 210°C, que é resfriado pela água passando pela mangueira.
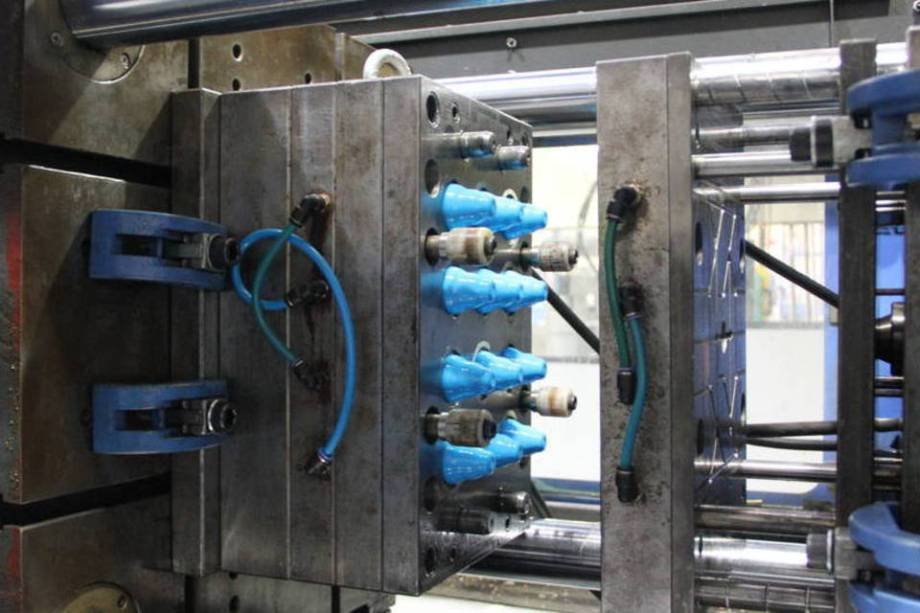
9 /20(Karin Salomão/Exame.com)
A cada 22 segundos, a máquina consegue produzir 12 capuzes. Por dia, são 47.127 capuzes, se a máquina não parar em nenhum momento. Em um ano, seriam mais de 17 milhões de peças.
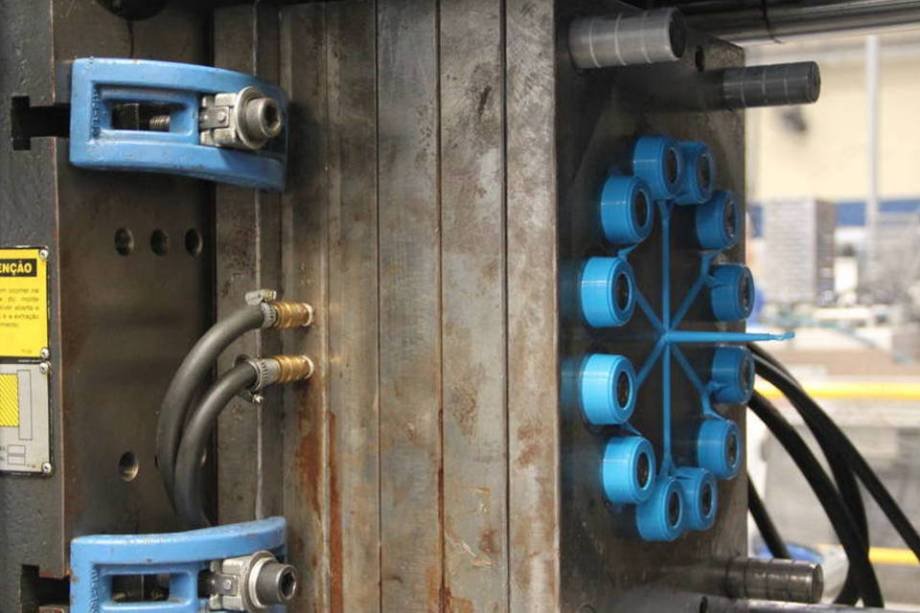
10 /20(Karin Salomão/Exame.com)
O mesmo processo de fabricação se aplica à rosca, que se encaixa no frasco e no bico da mamadeira. O material é derretido e injetado em um molde e posteriormente resfriado.
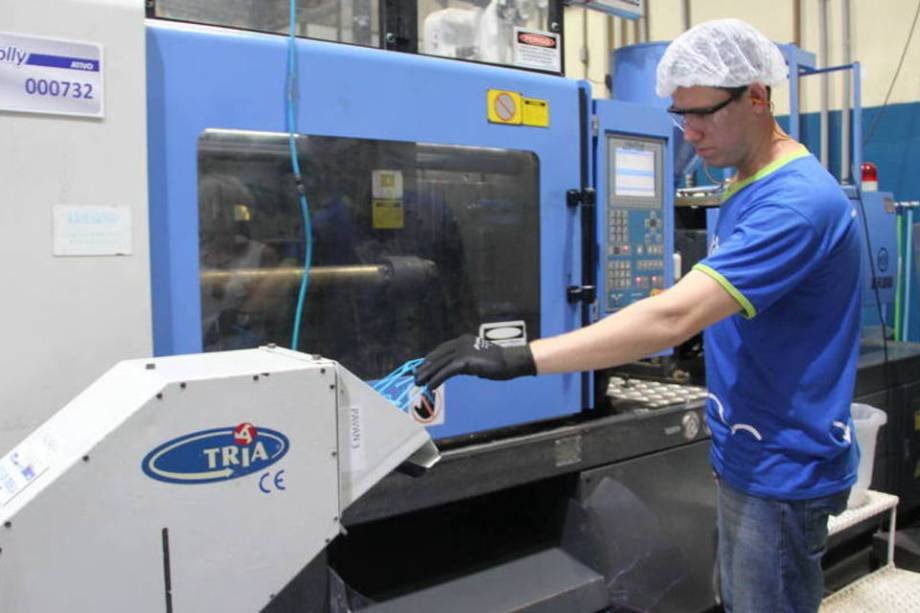
11 /20(Karin Salomão/Exame.com)
A resina passa por um filamento para alcançar cada um dos 12 moldes de rosca. O "caminho" pelo qual a resina passou também acaba secando. Para não desperdiçar, esse material é moído e reutilizado.
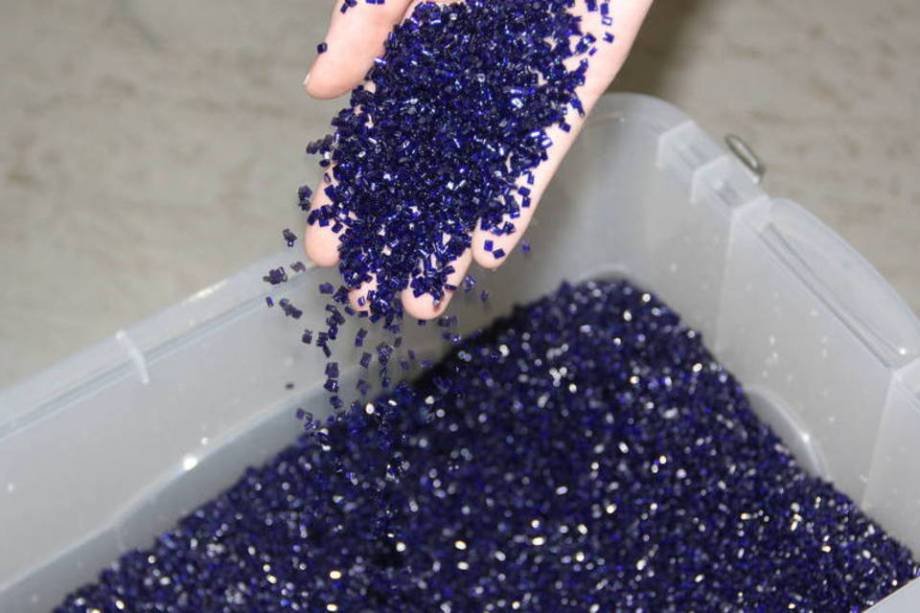
12 /20(Karin Salomão/Exame.com)
Normalmente, uma mesma máquina produz peças de pigmentações diferentes. Para facilitar a limpeza, a produção vai da cor mais clara, amarelo, por exemplo, passando pelo verde, azul, rosa, até chegar às cores mais escuras e com tingimentos mais fortes, como roxo, azul escuro e finalizando com o preto. Para trocar de uma cor para outra, a máquina roda algumas vezes para tirar qualquer resquício da cor anterior. Isso gera algumas peças manchadas, que precisam ser descartadas. A fábrica ainda estuda como facilitar esse processo e reduzir o descarte.
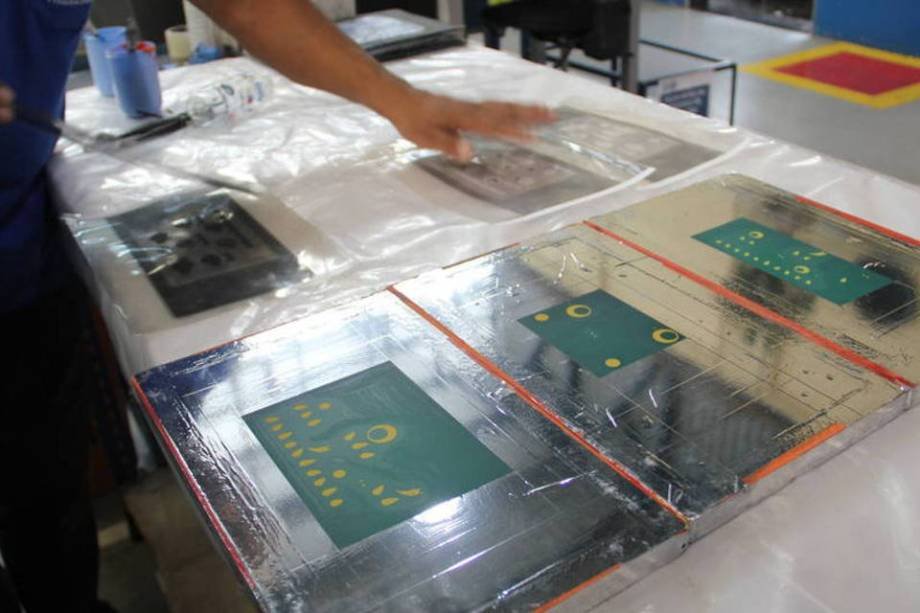
13 /20(Karin Salomão/Exame.com)
Para desenhar os caramujos coloridos desta mamadeira, são usadas seis cores. Cada cor tem uma tela, vazada exatamente onde a tinta deve ser aplicada.

14 /20(Karin Salomão/Exame.com)
Como a máquina só tem capacidade para três cores, a pintura é dividida em duas etapas. Aqui, já foram aplicadas as tintas branca, laranja e azul. Assim que a cor é pintada, a mamadeira passa por uma lâmpada de luz ultravioleta e seca imediatamente.
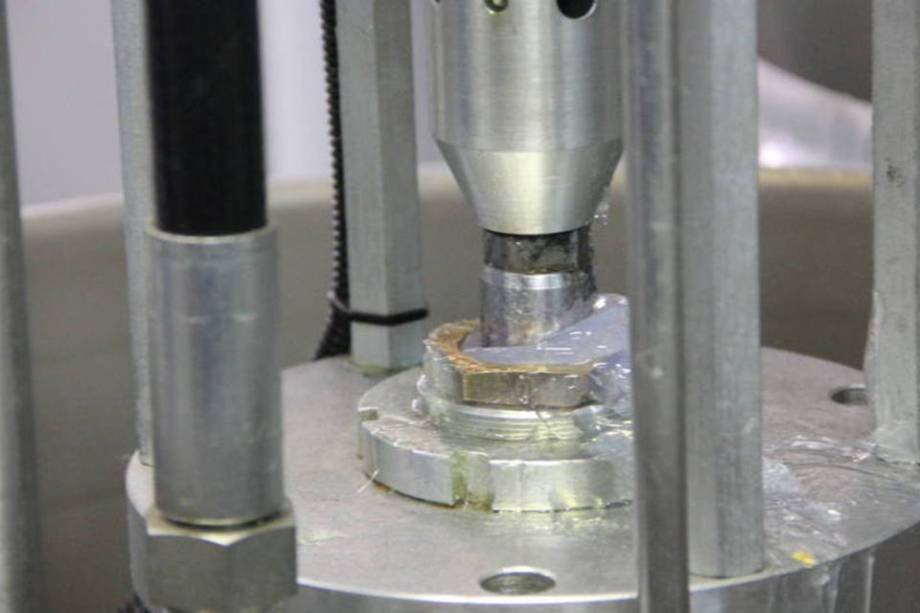
15 /20(Karin Salomão/Exame.com)
O último componente é o bico. Nesse caso, o material usado é silicone. A matéria prima chega dividida em dois componentes. Se eles entrarem em contato antes da hora, secam e endurecem.
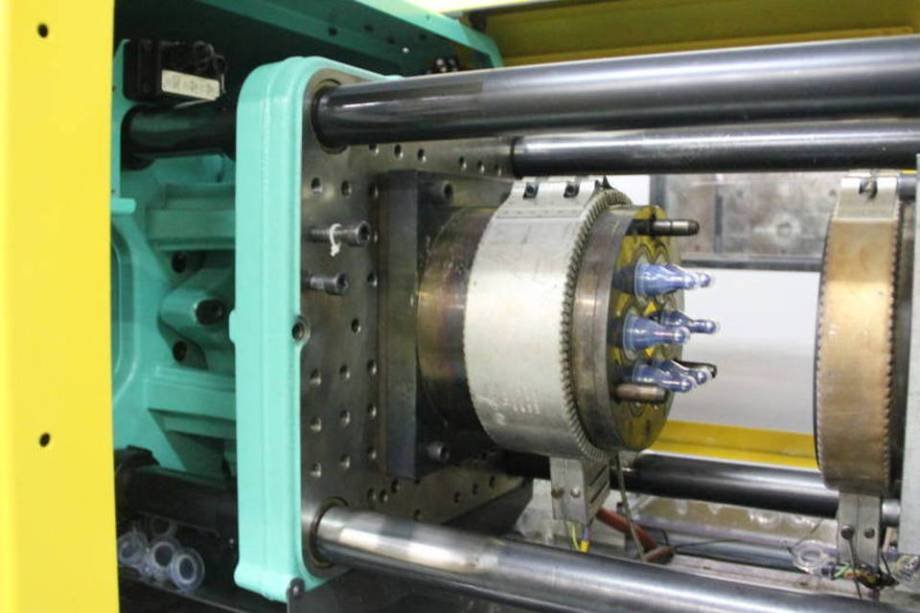
16 /20(Karin Salomão/Exame.com)
Os dois componentes só se encontram no tubo de injeção, momentos antes de chegar ao molde. Aqui, ao contrário dos outros processos, o material chega gelado a 5°C e o molde que é aquecido, a 185°C. Como silicone também é um material difícil de manipular, a Lolly importou essa máquina para fazer os bicos da mamadeira da Alemanha.
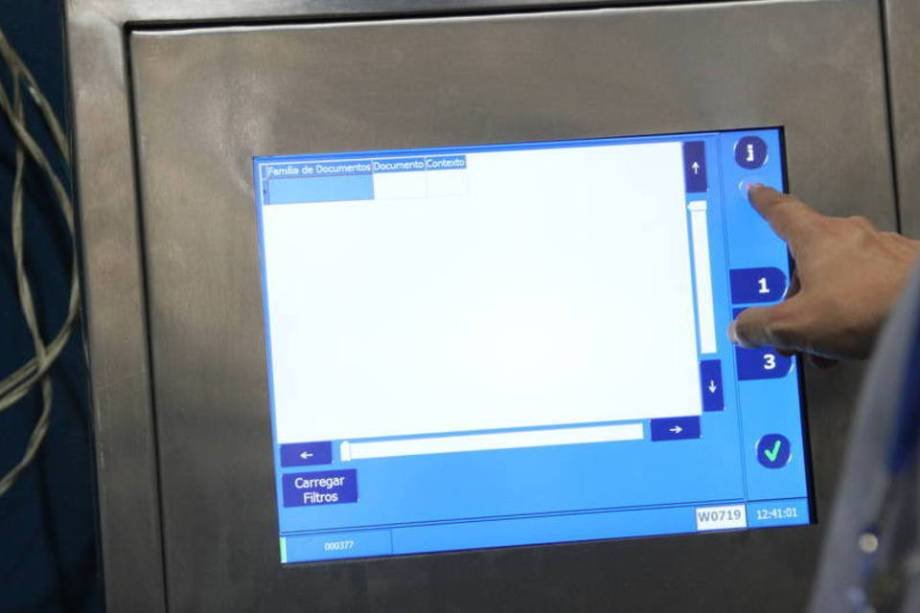
17 /20(Karin Salomão/Exame.com)
Para gerenciar todos esses processos, a área de Tecnologia da Informação da Lolly criou um sistema de gestão. Cada máquina tem o seu terminal, que informa qual o funcionário que a está operando e calcula produção, qualidade, eficiência e informa os motivos de parada. Em operação há quatro meses, o novo sistema de gestão já melhorou a produtividade da fábrica.
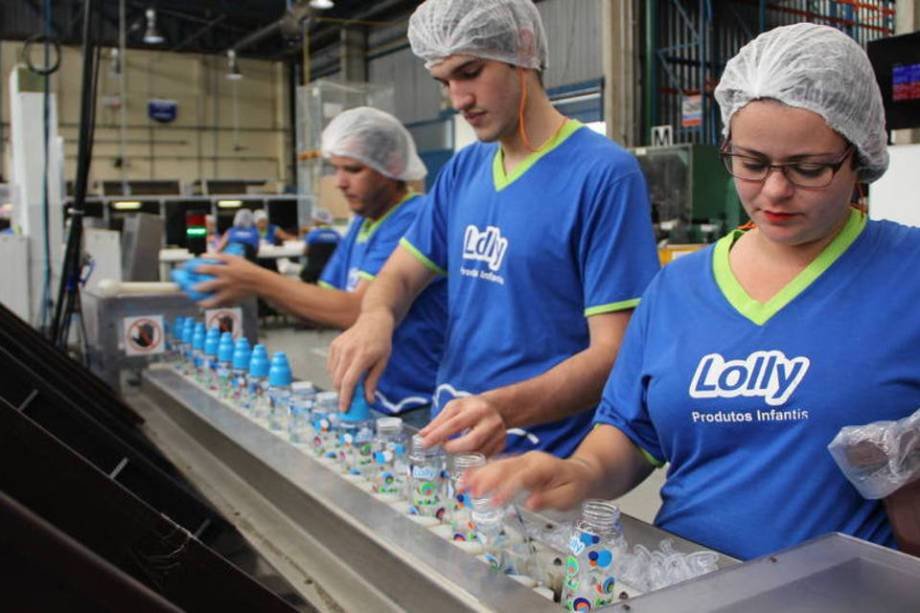
18 /20(Karin Salomão/Exame.com)
Todas as peças se encontram na montagem, feita em parte manualmente por três funcionários.
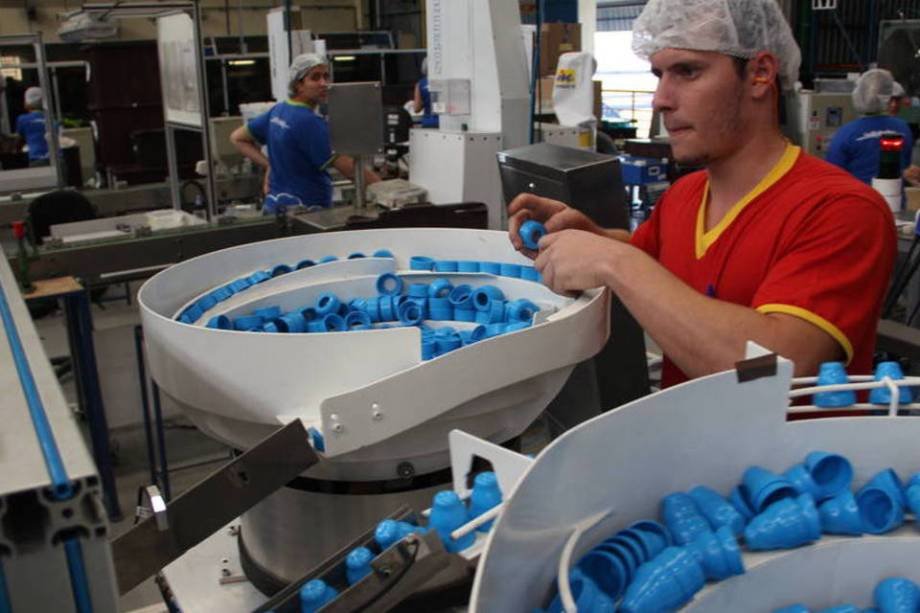
19 /20(Karin Salomão/Exame.com)
Recentemente, a equipe de engenharia da fábrica automatizou uma das etapas – encaixar o capuz na rosca. Assim, conseguiram acelerar a montagem – de 1200 mamadeiras por hora para 1500 - e redirecionar um dos 5 funcionários responsáveis pela montagem para outra área.
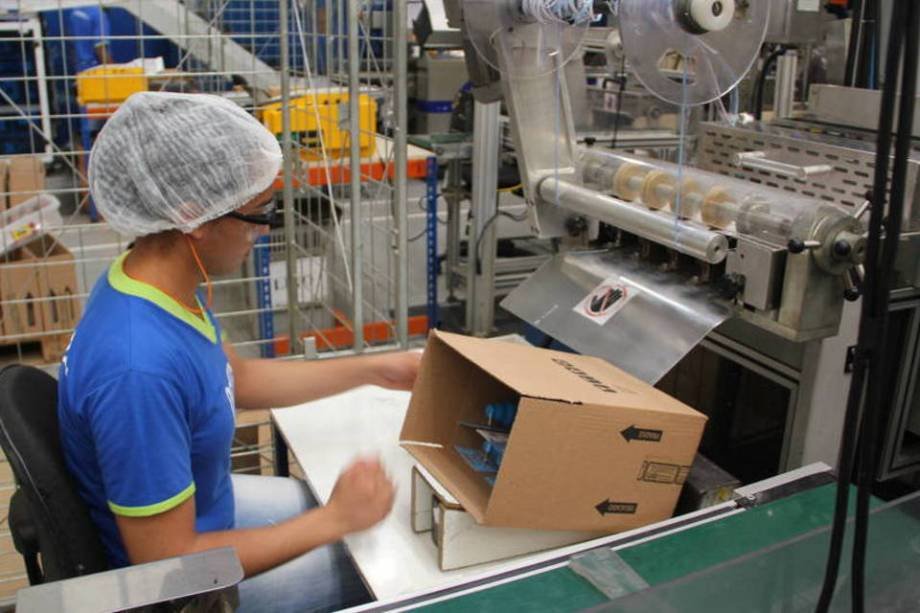
20 /20(Karin Salomão/Exame.com)
A última etapa é a embalagem, que prepara a mamadeira para ser vendida nas lojas.