BMW i3 feito com fibra de carbono traz mudança na indústria
O novo material representa a maior mudança na produção automobilística desde os anos 1980, quando os primeiros carros com estrutura de alumínio foram fabricados
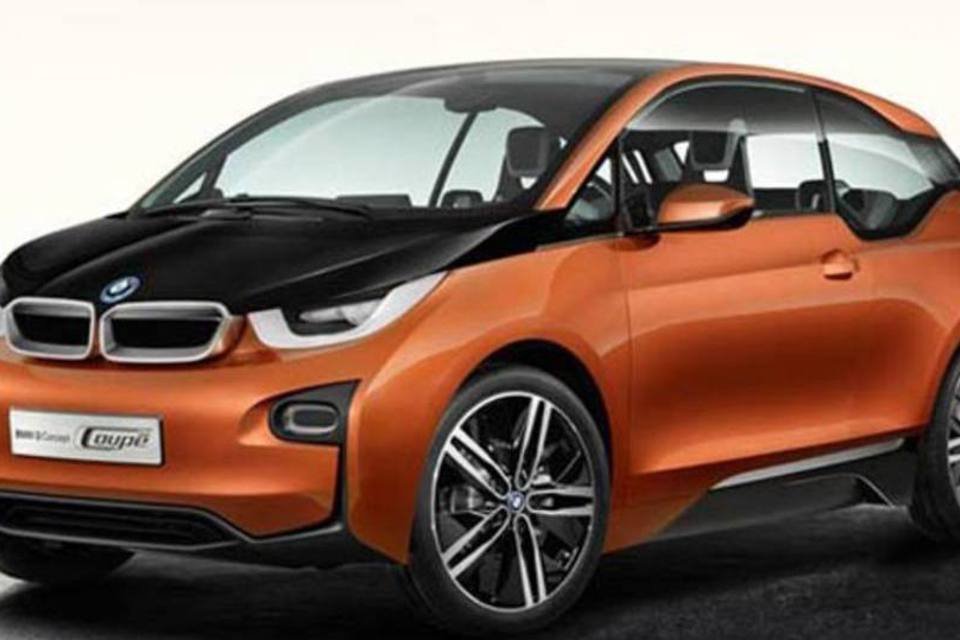
Da Redação
Publicado em 18 de novembro de 2013 às 06h34.
A aposta da Bayerische Motoren Werke AG, a BMW , para salvar seus carros de uma potencial extinção começa com centenas de milhares de fios brancos e finos serpenteando em uma sala de produção na zona rural de Washington.
Formando quase uma milha de extensão, o fio, que parece ser o espaguete mais fino do mundo, será esticado, torrado e eventualmente queimado para criar fibra de carbono -- um material mais fino que o cabelo humano e mais resistente que o aço.
A BMW usará os fios negros e elegantes para a estrutura do carro elétrico i3, que irá à venda nas concessionárias da Alemanha amanhã e ao redor do mundo nos próximos meses.
É o primeiro esforço para produzir em massa um carro feito principalmente de fibra de carbono e que representa a maior mudança na produção automobilística desde pelo menos os anos 1980, quando os primeiros carros com estrutura totalmente de alumínio foram fabricados.
A estratégia começou a ganhar forma seis anos atrás, quando Norbert Reithofer, na época o CEO recém nomeado, examinou tendências que estavam afetando a indústria e concluiu que uma maior preocupação com o meio ambiente provavelmente levaria a regulações mais duras sobre emissões, que poderiam tornar insustentável o futuro de carros como os sedãs Série 5.
Ameaças ao negócio
“Olhando para frente, para 2020, nós vimos ameaças ao nosso modelo de negócio”, disse o diretor financeiro Friedrich Eichiner, que chefiou o planejamento estratégico na época, em entrevista em seu escritório de mobília escassa no edifício-sede da empresa em Munique. “Nós tivemos que encontrar uma maneira de levar modelos como o Série 6, o Série 7 e o X5 ao futuro”.
Para que a BMW continuasse vendendo modelos que representam a autoafirmação da empresa de que o carro que produz é a “máxima máquina automotora”, a fabricante precisava compensar essas emissões com um carro elétrico viável para cidades em expansão, onde cada vez mais clientes potenciais viveriam. Foi assim que o i3 começou.
Na época, os carros elétricos tinham a fama de serem lentos porque a bateria, pesada, precisava ter uma carga capaz de mover o veículo por pelo menos 100 quilômetros -- a distância considerada necessária para o uso diário. Isso significava que o carro precisava ser mais leve para reduzir o tamanho e o custo do equipamento de energia e melhorar a direção. O material mais leve e forte disponível é a fibra de carbono.
Alto custo
O lado negativo é que ele é proibitivamente caro. A consultora Frost Sullivan estima que a fibra de carbono custa cerca de US$ 20 por quilo. O valor contrasta com o do aço, de US$ 1. A meta da BMW é baixar o custo da estrutura de fibra de carbono para o nível do preço do alumínio até 2020.
Embora os fios finos e negros tenham sido usados na Fórmula 1, em carros esportivos de elite como o Bugatti Veyron e em jatos 787 da Boeing Co., o material não foi testado em produções de larga escala por causa do custo e por causa do tempo e da complexidade envolvidos. Então a BMW planeja fazer o que ninguém mais fez: produção massiva de fibra de carbono.
“O investimento em fibra de carbono não é para um veículo, mas para o futuro de todo o nosso portfólio e, portanto, do nosso negócio”, disse Eichiner. “Não há maneira de tornar os carros mais leves e o aço está chegando ao seu limite”.
Na fábrica da BMW em Leipzig, o aço não é mais a medida de dureza. Em uma placa, por lá, lê-se a frase “nervos de fibra de carbono”. A empresa não tem medo de investir nisso sozinha.
“Quando você opta por um novo caminho, sempre há um risco”, disse Eichiner. “Mas se você tiver sucesso, é uma chance enorme, e a concorrência precisará de tempo para se atualizar. Não há muitas oportunidades nessa indústria para ganhar uma vantagem como essa”.
A aposta da Bayerische Motoren Werke AG, a BMW , para salvar seus carros de uma potencial extinção começa com centenas de milhares de fios brancos e finos serpenteando em uma sala de produção na zona rural de Washington.
Formando quase uma milha de extensão, o fio, que parece ser o espaguete mais fino do mundo, será esticado, torrado e eventualmente queimado para criar fibra de carbono -- um material mais fino que o cabelo humano e mais resistente que o aço.
A BMW usará os fios negros e elegantes para a estrutura do carro elétrico i3, que irá à venda nas concessionárias da Alemanha amanhã e ao redor do mundo nos próximos meses.
É o primeiro esforço para produzir em massa um carro feito principalmente de fibra de carbono e que representa a maior mudança na produção automobilística desde pelo menos os anos 1980, quando os primeiros carros com estrutura totalmente de alumínio foram fabricados.
A estratégia começou a ganhar forma seis anos atrás, quando Norbert Reithofer, na época o CEO recém nomeado, examinou tendências que estavam afetando a indústria e concluiu que uma maior preocupação com o meio ambiente provavelmente levaria a regulações mais duras sobre emissões, que poderiam tornar insustentável o futuro de carros como os sedãs Série 5.
Ameaças ao negócio
“Olhando para frente, para 2020, nós vimos ameaças ao nosso modelo de negócio”, disse o diretor financeiro Friedrich Eichiner, que chefiou o planejamento estratégico na época, em entrevista em seu escritório de mobília escassa no edifício-sede da empresa em Munique. “Nós tivemos que encontrar uma maneira de levar modelos como o Série 6, o Série 7 e o X5 ao futuro”.
Para que a BMW continuasse vendendo modelos que representam a autoafirmação da empresa de que o carro que produz é a “máxima máquina automotora”, a fabricante precisava compensar essas emissões com um carro elétrico viável para cidades em expansão, onde cada vez mais clientes potenciais viveriam. Foi assim que o i3 começou.
Na época, os carros elétricos tinham a fama de serem lentos porque a bateria, pesada, precisava ter uma carga capaz de mover o veículo por pelo menos 100 quilômetros -- a distância considerada necessária para o uso diário. Isso significava que o carro precisava ser mais leve para reduzir o tamanho e o custo do equipamento de energia e melhorar a direção. O material mais leve e forte disponível é a fibra de carbono.
Alto custo
O lado negativo é que ele é proibitivamente caro. A consultora Frost Sullivan estima que a fibra de carbono custa cerca de US$ 20 por quilo. O valor contrasta com o do aço, de US$ 1. A meta da BMW é baixar o custo da estrutura de fibra de carbono para o nível do preço do alumínio até 2020.
Embora os fios finos e negros tenham sido usados na Fórmula 1, em carros esportivos de elite como o Bugatti Veyron e em jatos 787 da Boeing Co., o material não foi testado em produções de larga escala por causa do custo e por causa do tempo e da complexidade envolvidos. Então a BMW planeja fazer o que ninguém mais fez: produção massiva de fibra de carbono.
“O investimento em fibra de carbono não é para um veículo, mas para o futuro de todo o nosso portfólio e, portanto, do nosso negócio”, disse Eichiner. “Não há maneira de tornar os carros mais leves e o aço está chegando ao seu limite”.
Na fábrica da BMW em Leipzig, o aço não é mais a medida de dureza. Em uma placa, por lá, lê-se a frase “nervos de fibra de carbono”. A empresa não tem medo de investir nisso sozinha.
“Quando você opta por um novo caminho, sempre há um risco”, disse Eichiner. “Mas se você tiver sucesso, é uma chance enorme, e a concorrência precisará de tempo para se atualizar. Não há muitas oportunidades nessa indústria para ganhar uma vantagem como essa”.